- On sale!
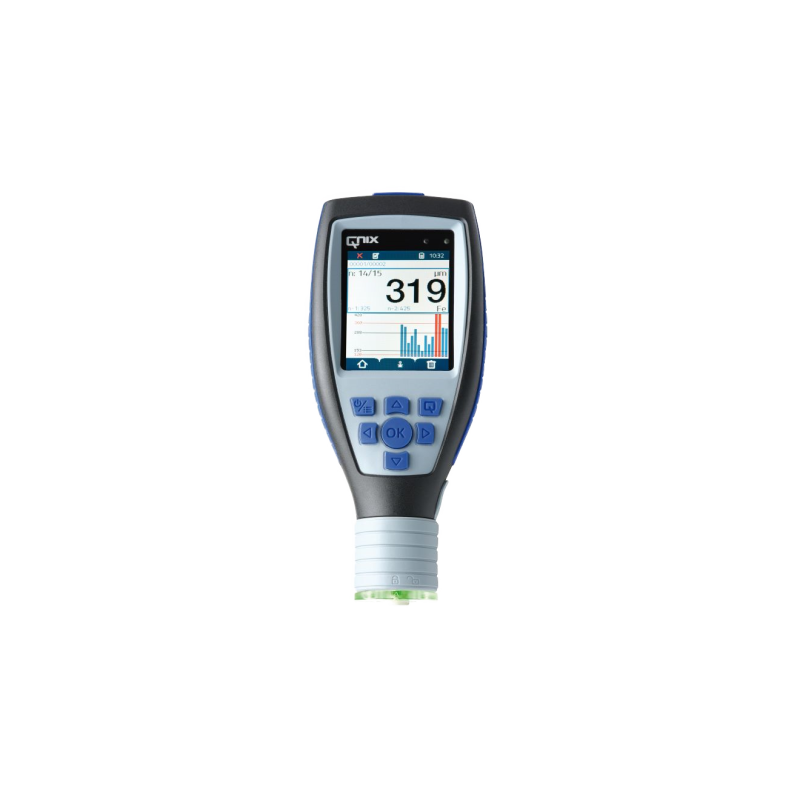





Automation Dr. Nix QNix® 9500 basic Coating Paint Thickness Gauges with integral probe Fe 50 mils is a rugged – IP protection IP64 and electronic digital Paint & Coating thickness gauge designed for fast (more than 120 readings per minute), accurate, reliable and repeatable dry Film thickness measurements on both ferrous metals: ISO/FE and NF/FE, .
QNix® 9500 coating thickness Paint Gauge F/NF with integrated probe
QNix® 9500 Thickness Gauge PC software is built-in the gauge body and not dependent on the current version of Windows
Conforms to DIN EN ISO 2808, DIN 50981, DIN 50984, ISO 2178, BS 5411 (3 & 11), BS 3900-C5, ASTM B 499, ISO 2360, ASTM D 1400, ASTM D 1186, ASTM D 7091
QNix 9500 premium plus version measures according to international standards such as SSPC-PA2 levels 1-5, IMO PSPC, Australian AS 3894.3, Swedish IS 184160, ISO 19840. The most frequently used standard for non-destructive measurement of dry film thickness on both ferrous and non-ferrous metals is the PA 2 of SSPC - procedure for determining conformance to Dry Coating thickness requirements. Founded in 1950, the SSPC – a steel structures planning council, is a not-for-profit association focused on the use of coatings to protect marine and industrial steel structures. PA 2 standard describes a procedure to determine whether dry film thickness over an extended surface area ( large and flat) conforms to the specified minimum and maximum levels.
PA 2 defines what a gauge reading is, spot measurement, and area measurement. Other important aspects of the PA 2 are the definition of calibration, verification of Dry Film Gauge accuracy, Gauge adjustment, and the measurement procedures. It further specifies the required number of measurements for conformance to a thickness, gauge principles, and factors that affect thickness measurement, such as surface roughness, tacky film, curvature, etc. Since gauge readings often differ even in close proximity, due to surface irregularities, it recommends that coated surfaces be sectioned into test areas and that a minimum of 15 individual measurements is taken in 5 groups of 3 spaced out measurements each.
Gauge Calibration according to PA 2 actually means factory calibration, also done by a qualified laboratory in a controlled environment following a documented procedure. During the calibration process, the manufacturer ensures that the gauge meets the accuracy specifications and issues a calibration certificate traceable to National Metrology Insitute. Whereas no calibration intervals are specified, a one-year interval is recommended. Verify the accuracy of the dry film Gauge with a traceable coating thickness standard. ASTM D7091 prescribes 3 operational steps to ensure accurate measurement (Calibration, verification, and adjustment). Gauges should be adjusted to the prevailing conditions to minimize surface roughness and curvatures.
QNix® 9500 series of Thickness Gauges is a rugged – IP protection IP64 and electronic digital Paint & Coating thickness gauge designed for fast (more than 120 readings per minute), accurate, reliable, and repeatable mil thickness measurements on both ferrous and non-ferrous metals and Dual probes on all relevant substrates: ISO/FE, NF/FE, ISO/NF. QNix® 9500 is ideal for single-handed operations and uses the proven Hall sensor technology (ISO 2178, ASTM D7091) to measure non-conductive, non-magnetic coating thickness on magnetic substrates such as steel, chrome, copper, zinc. Eddy current principle (ISO 2360, ASTM D7091) is used to measure non-conductive coating thickness on non-ferrous metals substrates. With its ability to interchange probes and statistically (graphic) display, the QNix® 9500 Mil Gauges covers almost all features of a more advanced Dry Film Thickness Gauge - Mil Gauge. Available probes for the QNix® 9500 Coating Thickness Gauge, which are either integrated or interchangeable with cable, are built with stainless and enclosed by a protective membrane IP65 for dust resistant (weatherproof). It has a polished ruby tip that is extremely wear-resistant. The QNix® 9500 DTF Gauge comes in three versions: Basic, Premium, Premium Plus, fully calibrated and is equipped with easily adjustable features for measuring on rough and curved surfaces. Its low center of gravity and extremely large contact surface ensures correct placement, better handling, and precise measuring results. It comes with a Certificate of Calibration traceable to a national metrology institute PTB.
QNix® 9500 coating thickness Paint Gauge F/NF with integrated probe
• Gauge body with built-in PC software QN9
• Fe- and NFe zero-reference plates and two test foils (shims)
• Certificate of Calibration traceable to PTB (only with integrated
measuring probe)
• Operation/User manual
• USB cable
• 2 Mignon batteries 1,5 V (AA) alkaline
• Plastic case for transportation and storage
All you need to know to properly use the QNix® 9500 Paint /Coating Thickness Gauge (Frequently Asked Questions- FAQs).
- Is the QNix 9500 Paint thickness gauge calibrated at the factory?
QNix 9500 Mil gauge comes ready to measure and factory calibrated. A Certificate of Calibration traceable to PTB is included that documents actual readings taken by the paint thickness gauge at our calibration laboratory in Cologne, Germany. For best measurement results, check gauge accuracy by simply zeroing on the to be used uncoated substrate.
- Does the QNix 9500 Paint thickness gauge measure coatings on stainless steel?
Stainless steel is used in manifold applications in different industries (automotive, cookware, tanks, cutlery, sinks, food, and beverage due to its formability –faced-centered cubic crystal structure, non-heat-treatable and excellent characteristic of resistance to corrosion- cold treated, hardness and stress resistance can be increased. The most common grade is Austenitic steels. These are non-magnetic stainless steels with high levels of chromium and nickel but low levels of carbon.
The QNix® 9500 - any version of the Paint thickness gauge with a dual (ferrous/non-ferrous) probe can measure on austenitic steel. However, zeroing on the uncoated steel is recommended.
- Does the QNix 9500 Paint thickness gauge measure nickel on steel?
Many industries use nickel plating, which is an important electrodeposition process to make steel, brass and other basis substrates more resistible to corrosion. Nickel plating is not only an excellent abrasion and corrosion-resistant, but it is preferred because it can be uniformly plated and it is a good surface lubricant.
QNix® 9500 Paint Gauge can measure electroless Nickel Plating – no addition of an electric current which is non-magnetic. QNix® 9500 will accurately measure the thickness of such plating on ferrous steel with a coating thickness gauge using a ferrous probe (magnetic principle: Magnetic field amendment/Hall-effect Fe).
There are three versions for the QNix® 9500 Paint Thickness Gauge: Basic, Premium and Premium Plus version. All three versions come with an integral probe or interchangeable probe with an extension cable for easy access to hard to reach measuring areas.
The integral probe version has a fixed probe to the gauge body and cannot be detached. The integral probe version is easily identified with its black probe grip holder. The modular probe version allows the probe to be detached from the gauge body. Identify the modular probe version easily with its grey probe holder.
There are considerable differences between these two versions of QNix 9500 Paint Thickness Gauge. The QNix® 9500 Mil thickness gauge premium plus has a higher storage capacity of up to 2,000,000 readings, 100 jobs with 100 areas each. The operator can create up to 100 jobs in 100 job areas with the QNix® 9500 premium+. Furthermore, each area can record up to 10,000 readings for documentation and evaluation on the PC. The QNix® premium+ Paint depth gauge has preconfigured adjustment settings for Limit settings, ISO 19840 Zero Offset, ISO 19840, ISO 19840 2-Point, SSPC PA2 (80/120), (Level 1-5), SSPC PA2 Zero Offset, IMO PSPC (90/10), SSPC PA2 2-Point, AS 3894.3 Australian, Swedish IS 184160. On the other hand, the QNix® 9500 Paint Thickness Gauge premium version has a capacity of only 1,000,000 readings storage and 1 job with 100 areas at most. It has the possibilities to perform 1- & 2- point adjustments. The job and job areas in both versions can be configured on the PC and the configuration transferred into the gauge body.
There are three progressive levels of decision making procedure for finding the right QNix® 9500 paint thickness gauge version for your application:
Level 1:
The operator is interested in fast, time-saving measurements and wants the live statistics shown and values or a graphic.
The operator wants to store limited data on the gauge body and use the in gauge body inbuilt Software to evaluate readings and manage data.
The operator wants to be able to perform zero, 1 & 2- point adjustments.
RECOMMENDATION: QNix® 9500 Paint Thickness Gauge Basic.
Level 2:
The operator is interested in fast, time-saving measurements and wants the live statistics shown and values or a graphic.
The operator wants to store limited data on the gauge body and use the in gauge body inbuilt Software to evaluate readings and manage data.
The operator wants to be able to perform zero, 1 & 2- point adjustments.
The operator wants to measure individual thicknesses of both paint and zinc galvanize layers with a single reading – Duplex coating system.
The operator wants to adjust memory in gauge body( up to 10 adjustments possible)
The operator is interested in fast, time-saving measurements and wants the live statistics shown and values or a graphic.
The operator wants to store limited data on the gauge body and use the in gauge body inbuilt Software to evaluate readings and manage data.
The operator wants to be able to perform zero, 1 & 2- point adjustments.
The operator wants to adjust memory in gauge body( up to 10 adjustments possible)
The operator wants to measure individual thicknesses of both paint and zinc galvanize layers with a single reading – Duplex coating system.
The operator has to adhere to industry standards by using the preconfigured adjustment settings for Limit settings, ISO 19840 Zero Offset, ISO 19840, ISO 19840 2-Point, SSPC PA2 (80/120), (Level 1-5), SSPC PA2 Zero Offset, IMO PSPC (90/10), SSPC PA2 2-Point, AS 3894.3 Australian, Swedish IS 184160
RECOMMENDATION: QNix® 9500 Paint Thickness Gauge premium plus.
While the inherent features of the Paint Gauges – basic, premium, premium plus, will make no difference as to the scope of supply, it is dependent on whether you ordered an integral probe or modular probe version of the QNix® 9500 paint thickness gauge.
Integral probe QNix® 9500 DFT Gauge scope of supply: Gauge body with fix probe QNix® 9500, PC Software QN9, Zero reference Fe and Non-Fe plate with two uncertified test foils (shims), Test/ Calibration certificate showing traceability to PTB, operation/ user manual, USB cable, 2 Mignon batteries 1,5 V (AA) alkaline, a plastic carrying case for safe device transportation and storage
Modular probe QNix® 9500 Mil Thickness: scope of supply: Gauge body QNix® 9500, PC Software QN9, Zero reference Fe and Non-Fe plate with two uncertified test foils (shims), Test/ Calibration certificate showing traceability to PTB, operation/ user manual, USB cable, 2 Mignon batteries 1,5 V (AA) alkaline, a plastic carrying case for safe device transportation and storage, - probe adaptor cable for extending the probe, probe holder, measuring probe.
Use one hand to hold the gauge body and then with the other hand turn the probe to the left to open- anti-clockwise. At this position, please pull the probe with the probe holder out of the gauge body.
You can then install the probe you intend to use next by inserting it into the holder. If you are using the extension cable, do the same and insert both and lock tight by turning it to the right - clockwise.
Note that all standard probes used with the QNix® 9500 Mil Gauge are as well compatible with the QNix® 5500 Paint gauge.
To begin, take both probe and probe holder out off the Gauge body if they were previously used inserted or out of the plastic carrying case, if not connected to the gauge body. Then Screw the probe together with the probe holder in the adaptor cable and finally connect the other end of the extension cable to the gauge body.
We have made life easy for you! A digital copy of the actual calibration certificate is stored in the probe and can be retrieved with your software. Now you can also include actual calibration certificate via QN9 Desktop/Mac software to your reports.
Display Information
- The display allows for quick and intuitive navigation through the measuring process.
- The lower part of the display allows the operator to switch between a graphic and reading showed as basic statistical data.
- The middle of the display is the reading area. It allows the operator to observe each reading of the temporarily saved measurements or navigate the activated area. There, incorrect readings can be deleted.
- With the upper position of the display, you alter- depending on the gauge body version, the areas of a job.
How to Set Limits on the QNix 9500
Turn on the Gauge by pressing the left button, then press the same button again twice to see four navigation tabs. Use the right arrow button to switch to the red tab- which is the tab for setting limits and averaging. The operator can choose the limit type by pressing the “OK” bottom, while on “Limits off”. The following options are indicated: No limits“ means limit and average values are deactivated, „Simple limits“ for maximum, minimum, average, automatic range, individual, ISO 19840, IMO PSPC or SSPC PA2 Level 1-5 (Premium+)
How do I create a job (Premium+)?
Turn on the Gauge by pressing the left button, then press the same button again twice to see four navigation tabs. The first tab is where jobs can be created. navigate to the blue tab for jobs Choose „New Job“, then Choose „New empty job“, to create a new job. You can create job templates via the QN9 desktop/Mac software and transfer them to the gauge body. With the job templates, you define job areas in advance, assigning names and limits for a job, and for every area within that job.
Turn on the Gauge by pressing the left button, then press the same button again twice to see four navigation tabs – navigate to the blue tab for jobs then choose a job and choose „New area“. The area is created immediately. Choosing the „Activate area “, will save your readings for that area.
Turn on the Gauge by pressing the left button, then press the same button again twice to see four navigation tabs – navigate with the right arrow to the orange tab for adjustments. Go to “Settings“ and choose the mode of adjustment - „Zeroing“ is a standard reference gauge adjustment to zero), Averaging gives you the basic statistics on the display. „1-Point adjustment“ is carried out with certified calibration foil within or nearest to the coating thickness to be measured). 2-Point adjustment“ is carried out with two certified calibration foils within or nearest to the coating thickness to be measured). The “Individual“ adjustment uses any number of calibration foils (1-5) within or nearest to the coating thickness to be measured.
Adjustment Paint Gauge according to ISO 19840 or SSPC PA2 (premium+)
Turn on the Gauge by pressing the left button, then press the same button again twice to see four navigation tabs – navigate with the right arrow to the orange tab for adjustments. Go to “Settings“ and choose the mode of adjustment - „Zeroing” then press OK. A list of adjustment s will be indicated. Scrow down to choose the desired standard of measurement to comply with. Remember you can compensate for surface roughness by moving from zeroing and scrolling down to the roughness feature.
No customer reviews for the moment.